Thermal Imagers and the Industrial Fire Brigade
Troubleshooting, first aid, and hazmat incidents are three applications where imagers can speed up a response.
THERMAL imagers (TIs) are sweeping through the North American fire service as more and more municipal fire departments adopt the technology. The Federal Emergency Management Agency recently reported approximately 25 percent of municipal fire departments have TIs. Anecdotal evidence indicates the adoption rate in industrial fire brigades (including industrial fire departments) has been much lower.
Municipal fire departments regularly justify TIs by explaining the advantages they bring in fire attack at a structure fire or during search and rescue. Industrial fire brigades (IFBs) may mistakenly believe that TIs are helpful only in fire safety organizations that respond to lots of fires, or that they help only in incidents involving fire. This article will provide IFBs with several realistic and valuable uses for TIs, only two of which actually involve fire.
What is a TI?
Prior to understanding why a TI is helpful to the IFB, one should understand exactly what a TI is and does. In short, a TI is a device that detects relative differences in surface temperature. These relative differences in temperature are converted into an electronic signal and shown on a display for the user to see. Thermal imagers are sensitive to 1/20th of a degree Celsius.
In many respects, the detector in the TI is similar to the human eye. Both the TI's detector (called a focal plane array, or FPA) and the eye are receivers; they receive energy and convert it into an image for our brains to interpret. The eye receives wavelengths of energy called "visible light," while the FPA receives wavelengths of heat energy called "infrared."
As with radio frequencies, different wavelengths of energy have different properties. Light energy passes easily through windows but does not pass through dark plastic bags, which are high in silicone content. A person looking through a window will see what is behind the window, while a person looking at a plastic bag will see only the color of the bag, not what is behind the bag. Silicone is somewhat transparent to infrared energy, so a TI will identify surface temperatures behind the plastic bag. Glass, however, is not transparent to infrared. For the most part, glass reflects infrared energy and thermal signatures. Photos 1 and 2 demonstrate how light and infrared behave differently.
Photo 1. Silicone is somewhat transparent to infrared, so a thermal imager identifies surface temperatures behind a plastic bag.
Photo 2. Glass is not transparent to infrared, but it is transparent to light. The thermal image shows the reflection of the user.
Despite the rare transparent material, the human eye and the TI do not "see" through most materials. Drywall, plaster, concrete, steel, wood, paneling, down comforters, doors, sofas, and the like are not transparent to visible light or infrared. The human eye and the TI "see" only what is on the surface--colors for the eye, temperature differences for the TI.
The TI and the Hunt for the Bad Ballast
Many manufacturing employees have experienced the frustration of hunting for overheated electrical equipment. The odor permeates the area and may even help narrow the search. Fluorescent light ballasts are among the most commonly overheated types of electrical equipment. The current method of searching for the bad ballast is a frustrating matter that involves feeling each light fixture for excessive heat. With ceiling heights of eight, ten or even 20 feet, this can be a challenge.
The TI can make the IFB's job much easier. By showing the relative surface temperature difference, a thermal imager can help identify bad ballasts, overheated outlets and any number of electrical problems. Because faulty electrical equipment increases current impedance, it becomes hotter than normal equipment. This difference is normally transmitted to a surface material, whether a light fixture or an outlet plate, making it "visible" to the TI.
For some types of equipment, a TI with an adjustable iris control or a temperature measurement device may be required in order to detect minor temperature differences. As with a light ballast, if electrical equipment is normally hot in an ambient environment, IFBs may have trouble differentiating "good" from "bad." By adjusting the iris manually or by using a temperature measurement device, the user should be able to detect malfunctioning equipment.
A real-life example comes from Belchertown, Mass. In 1999, firefighters were called to the local United Methodist Church where Girl Scouts were having an afternoon function. The group smelled something burning in the church building and couldn't pinpoint the source. Firefighters were led to a classroom on the second floor where the smell was strongest. Firefighter Mark LaVallee quickly scanned each row of fluorescent lights, looking for temperature variation. All of the lights showed as gray on the thermal imager screen until he pointed at a light in the far right corner of the room that showed as gleaming white. He immediately dismantled the light and found the high-temperature plastic housing surrounding the ballast had liquefied, confirming the source of the problem.
"If the thermal imager hadn't been available, we would have been responding to a fire within an hour at that location," said LaVallee. "And we would have had 40 Girl Scouts to evacuate. Instead, we had a calm situation, and none of the girls even knew that there was a problem."
The TI and First Aid
Oddly enough, the latest and greatest tool for firefighting actually has potential uses in emergency medical treatment. Because the TI senses relative differences in surface temperature, it can help find amputated digits or limbs that may not be visible to the human eye. Poor lighting conditions can reduce the search for an amputated part to a long, fruitless effort on hands and knees. Not only does this situation place rescuers and helpers at risk for accidentally crawling through bloodborne pathogens, but it also exposes them to the risk of injury by debris on the floor or nearby obstacles.
Amputations that occur in and around heavy machinery pose hazards to rescuers, as well. Lathes and presses may leave sharp scrap material, shavings, or splinters. Photos 3 and 4 illustrate how difficult it would be to find amputated fingers (simulated for this photograph) near a lathe without the aid of a TI. A rescuer forced to dig through all the shavings to find the fingers could be injured. Assuming the TI is brought into use quickly, the temperature of the amputated digits should be different enough from the surrounding materials that it may save minutes in the search efforts. Of course, the quicker the search, the more likely it is that a patient can expect successful reattachment of the body part.
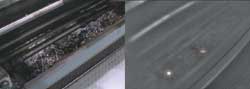
Photo 3. Metal shavings from a lathe hide "amputated fingers" from visible light.
Photo 4. A thermal imager identifies two warm areas underneath the metal shavings. These are the "amputated fingers." The red circles were added digitally for clarity.
The TI and Hazmat
Any IFB protecting a facility that regularly uses liquid or solid chemicals in its processes could benefit from having a TI. Proper use of thermal imaging can help identify product levels in sealed or pressurized containers and can help identify the source and extent of a product leak.
Because most liquids and solids heat and cool at different rates than air, TIs can frequently detect temperature differences on the surface of a container. While the liquid or solid inside is one temperature, the vapor space in that container may be a different temperature. If there is a temperature difference and the container is not insulated, the product level should be evident on the screen of the TI.
Photo 5 shows two five-gallon pails. Because the liquid inside is cool and the vapor space has heated up as the day has progressed, the liquid level is evident. These standard pails, as one might expect, are not insulated. This makes even slight temperature differences on the surface of the pails evident to the TI. (Note that if these pails had been in a stable, unchanging environment for an extended period, the product level would not be evident. If the product, the vapor space inside the container, and the container itself are all equalized in temperature, then there is no temperature difference for the TI to detect.)
Keep in mind, however, TIs will not show the presence of gases. There may be exceptions for dense concentrations of very cold or very hot gases.
Photo 5. Two five-gallon pails each show they are about half-full of product. There must be a temperature differential between the material and the vapor space for this to be effective.
The TI and Boilover
Just as the TI can show product levels in hazmat incidents, it can help predict the approach of boilover at a crude oil facility fire. Boilover occurs after a "heat wave" moves through the product in a storage tank. The lighter products of crude oil burn rapidly, heating the heavy radicals to temperatures above 200° C (392° F) without bringing them to their flashpoints. The heaviest ends, which are in contact with the water in the storage tank, reach this temperature and cause the water to exceed its boiling point. The boiling water turns into steam, expanding its volume by 1,700 times. This forces the burning product out of the tank in a violent explosion.
If an IFB monitors a burning tank by using a thermal imager, it could see the progression of the heat wave through the tank. As the heavier ends are heated and drop within the tank, the walls of the tank should be heated, as well. Through judicious use of the TI, an IFB may be able to determine where the heat wave is within the tank. As the wave nears the presumed (or known) water level, the IFB can effect the necessary evacuations to ensure any boilover does not injure firefighters.
There is a note of caution here: Metal can trick a TI. Because metals tend to reflect the temperatures around them rather than showing their own temperatures, storage tanks may pose a challenge in image interpretation. If an IFB is unfortunate enough to confront an oil tank fire, it must be careful not to fool itself into seeing things with the TI. Users must be willing to admit, if it is the case, that they cannot see the heat wave developing.
The TI and Structure Fires
Municipal fire services are rapidly discovering the need for TIs in structure fires. TIs dramatically improve a hose team's ability to find a fire, direct a hose stream properly, and monitor structural integrity. Search and rescue operations see 75 percent reductions in time, with up to a 90 percent improvement in success rates.
TIs also can help firefighters with ventilation and overhaul efforts. For IFBs that are actively involved in fire suppression, the TI can yield the same benefits. Hose teams will advance to the seat of the fire faster and safer, while placing their water more effectively on the fire. This can save the business significant amounts of money by reducing fire damage with a quick knock-down and by reducing water damage as a result of efficient hose deployment.
Even if an IFB acts more as a fire safety organization than a fire suppression organization, it can benefit from TIs. Members of the IFB can use the TI to scan large areas at risk of fire or smoke involvement to ensure all employees have evacuated. In the case of a large, active fire, a TI may help ensure employees are out of danger well before the municipal fire department arrives.
Conclusion
Considering that a TI can be helpful in situations from first aid or EMS, to hazardous materials releases, to structure fires, IFBs should first consider how these tools could play a role in their emergency operations. Leaders can help justify the purchase of a thermal imager by presenting some of the application scenarios that could be experienced in the industrial plants the brigade covers. Properly deployed, a thermal imager can pay for itself in one emergency operation by preserving the life or limb of a fellow employee or by saving critical assets of a facility.
This article originally appeared in the April 2004 issue of Occupational Health & Safety.