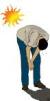
Walking the Path to Effective Controls
Milliken applies the DMAIC model to tackle heat stress in its operations.
- By Cati Spencer
- Mar 01, 2013
It's time to apply an uncommon approach to the common, high-risk occurrence of heat stress in our work environments. Most think of continuous improvement in the context of their quality programs, but the DMAIC model of Define, Measure, Analyze, Improve, and Control can play in several sandboxes.
Milliken broadens the application of continuous improvement work to include process development and control measures affecting all associates' safety. In fact, the company's 39 manufacturing sites have successfully applied the DMAIC thought process to safety for more than two decades. Headquartered in South Carolina with many manufacturing sites in the hottest states in the nation, Milliken provides solutions for linking existing processes, such as continuous improvement, to provide proactive solutions to any and all safety hazards. An analysis of how Milliken successfully tackles heat stress is instructive to those working in similar high-risk environments, while the application of continuous improvement methodologies to address all safety issues is relevant to everyone.
Define
Heat stress can be fatal. If healthy, well-trained athletes in the prime of their lives sometimes die on football fields because of dehydration and heat exhaustion, what must you do to address this workplace hazard in your sites? The first step is to define your risk potential. If heat is not a problem, consider other extreme conditions. Directing oil exploration in the polar climate of Barrow, Alaska, for example, reveals a different set of extreme conditions that may be similarly tackled using the DMAIC model.
At Milliken, we start every project by understanding what the site-specific data exposes as the greatest risk. You can transform your lagging indicators into predictive, leading measures by conducting incident profile analyses. Milliken's databases are populated with investigation facts from every near miss, first aid, and recordable incident investigation. We recommend analyzing your data trends in order to drill down to a high-risk department or even one particular piece of equipment. We find that narrowing the project scope in this way allows Milliken's safety leaders the ability to apply focused improvement efforts, while ensuring the highest risk issues are addressed first.
Holding more than 2,200 U.S. patents and 5,000 patents worldwide, our manufacturing is extremely diverse. No two locations among its sites are the same. A past evaluation of our incident profile analyses underscored the need to address the highest-risk areas. Then data were clear: Heat stress was a heightened risk at non-air conditioned locations utilizing high heat finishing ranges. Milliken associates working in these locations were at the highest risk to suffer from heat stress, and if no action was taken, leading indicators predicted that one or more associates would suffer a heat stress injury or illness during the summer months. As a result, focused continuous improvement projects were rolled out at these sites, reducing the risk of heat stress. Cross-functional teams of production associates serving various roles across the site were deployed to apply the DMAIC principles to reduce the risk of this hazard.
Measure
During 2010, OSHA reported 2,365 recordables caused by heat stress or stroke. Among these were fatalities. Using well-accepted statistical multipliers, we know that for every major incident there are 29 minor/first aid incidents and 300 near miss occurrences. Considering this multiplier, 2,365 OSHA heat-stress related recordables are equal to 68,585 heat-stress related minor/first aid incidents and another 709,500 near misses.
Milliken plants have emphasized the need for reporting all types of incidents in order to have accurate, reliable data to direct project work. For the purpose of your continuous improvement projects, we have learned that identifying your key leading metrics allows you to qualify early whether your project improvements are trending toward success. Lagging metrics only allow you to react. Utilizing near misses, environmental temperatures, and body temperatures of at-risk associates as key leading indicators allows you to change your project approach to keep it on track and proactively reduce risk. Early in the project, measurement of these important leading indicators creates a frame of reference for goal setting, aids the project team in the next project phase, and provides a baseline for comparison after improvements are complete.
Analyze
This phase of the continuous improvement project requires your project team to understand the problem and analyze the associated risk. Heat stress occurs when the body is unable to efficiently maintain its internal temperature. A body's normal cooling processes occurs through blood circulation to the skin and by sweating. However, when external temperatures are higher than the body temperature, or the environment is too humid for sweat to evaporate, the body cannot effectively release heat. The retention of this excess heat causes symptoms of disorientation, illness, loss of desire to drink, and possibly death.
Hazard risk assessments are utilized to determine the risk of individual job tasks by understanding the severity, frequency, and likelihood of heat stress for affected individuals. This allows your team to focus on specific job tasks that need attention. We recommend using Why-Why analyses to further understand the true root cause of associated risks. Further, Milliken recommends applying a 6M "gut check" to the Why-Why tool to ensure you fully consider all contributing factors of man, method, machine, material, Mother Nature, and measure.
Improve
After you have analyzed and determined root causes, we recommend your project team assign countermeasures to address specific risks and evaluate what effect those countermeasures will have on risk reduction. Awareness campaigns during high-risk months, improved PPE in the form of highly breathable and comfortable work wear, and environmental and body temperature monitoring programs were all countermeasures that were implemented by our heat stress teams.
Just as in quality applications of continuous improvement, the strength of your countermeasures has a significant impact in the success of the project. We challenge each project team to climb the countermeasure ladder. Raising awareness is the first step on this ladder and is the most basic countermeasure. Of course, education on heat stress, how to identify symptoms, and how to respond is valuable. But Milliken has learned that pairing fun activities with awareness initiatives increases the retention of critical information. We suggest you post the symptoms of heat stress near your site's high-heat areas. Challenge your associates to find these postings and turn them in for a refreshing prize, such as a cold sports drink or ice cream sandwich.
Auditing is the next rung on the countermeasure ladder. We utilize quick yet comprehensive audits covering a wide variety of topics throughout each site. Audits are modified on a regular basis to refocus on high areas of risk and to ensure new practices or procedures are followed. For heat stress reduction, job rotation, body temperature monitoring, and task time-limiting procedures are countermeasures that are added to audits. One rung up from auditing is visual controls. Temperature alert lights and caution signs in high-risk areas serve as visual reminders to raise awareness of heat stress risk areas.
The final three steps on the countermeasure ladder are installation of fail-safes, elimination of the task when possible, and automation. To ensure the quality of our finished product, Milliken's ranges are required to operate at high temperatures, so teams worked to review automation and "leaned out" work processes to minimize time spent in this adverse environment.
Control
Control is the final and most crucial step to your continuous improvement projects. A strong control plan should allow your team to positively answer the question, "Will this plan prevent this injury from ever occurring in this site again?" If it does not meet this standard, then work remains to be done. Control plans include reviews of audit results, monitoring programs, scheduled awareness events, and best-practice sharing events. This activity at Milliken closes the loop on heat stress and ensures our plants will be working in the realm of proactive prevention.
We recommend establishing your goal of zero incidents when initiating your safety continuous improvement projects.
Through the engagement of production associates in project teams, safety auditing, awareness activities, and the overall safety process, the Milliken culture has evolved to be a predictive, preventative process with 100 percent associate engagement. Application of existing continuous improvement methods to safety hazards in your own sites will aid in standardized use of tools. Inclusion of production associates in this process will give you the avenue to tap into their creative resources, increase engagement, and make improvements in matters that will have the most significant impact to them, their co-workers, the plant, and your company.
This article originally appeared in the March 2013 issue of Occupational Health & Safety.