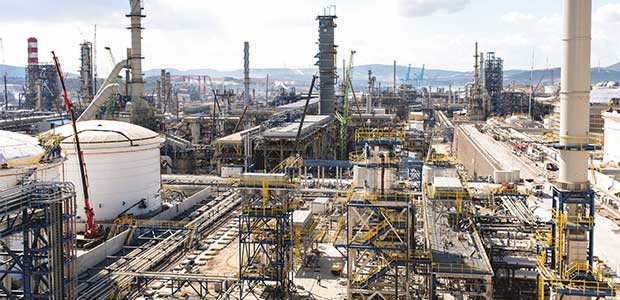
Optimize Large Scale Construction and Turnaround Projects through Data
How data science helps to keep construction and maintenance projects on schedule and within budget.
- By Igor Avlijas
- Sep 01, 2020
Construction and large-scale facility maintenance projects are significant undertakings and every task must be carefully orchestrated to avoid unexpected, and costly, delays. New construction of an industrial facility, such as a refinery or a power plant, shares similarities with subsequent major maintenance projects—a nearly endless list of specific tasks and an enormous number of specialized trades that deliver the manpower to make the project happen.
For greenfield construction, it is critical that the project is efficiently managed so operations can begin without delays. For turnarounds, unexpected delays can mean hundreds of thousands per day in lost revenue, or more. This extended time on the job could also lead to more opportunity for workers to face safety hazards, increasing the risk workers’ face when working on a construction site. Data science has emerged as a key tool to help project management teams minimize unexpected cost growth while increasing schedule confidence.
For these types of projects, the correct people, tools and resources must all be used in the right place and at the right time to ensure success. Project managers do everything they can to control the project outcome by trying to keep up with every current activity. Without key insights into what is really happening in the field, decision-making can lose elements of the bigger picture. To keep these projects on track, real-time decision making requires complete situational awareness that only data science can achieve.
Getting More from Data
Digital transformation is underway throughout the industry with connectivity and data at the core. Data science brings a broad range of sources together to empower practical decision-making. With interest in digitizing processes, businesses are increasingly finding value in connecting their workers using wearable technology as well as investment in people, their workflows, quality and performance. This technology has already become a staple for safety programs and is now playing a more prominent role in ensuring business efficiency and quality.
Cloud-connected worker wearables use wireless communications to connect personnel to their organization. Increasingly used for project management and workforce orchestration, these wearables are proven in evacuation and emergency response management, gas detection and lone worker monitoring. These devices can also support team collaboration like a walkie-talkie while also streaming information about an employee’s location, environment and overall health to a central location.
Data communicated to the cloud is securely stored and processed, providing exclusive access to select user roles within the business. Using data analytics tools, data scientists can crunch the data to present visuals to project management and operations teams, delivering actionable insights and alerts in real time through interactive dashboards. For example, worker wearables make it easy to see where teams are, to coordinate efforts and more quickly respond in unexpected situations. This mitigates against potential project delays and can save both time and money.
By leveraging data science in construction and major maintenance projects, construction managers can identify where productivity blockages (such as material availability, equipment utilization or permitting issues) occur and set performance benchmarks grounded in fact. This level of visibility enables managers to proactively orchestrate work-fronts, knowing the upcoming tasks and real-time locations of a vast number of workers and resources. Safety incidents, near misses and observables can be geographically mapped and checked against worker density or equipment movement to drive training, signage and team orchestration to reduce their occurrence.
Keeping it Lean
Leveraging data can also help companies adopt four of the eight LEAN Construction principles—reducing waste generated by waiting, transportation, unused talent and motion. LEAN Construction methodology seeks to create an efficient work environment by removing obstacles. Studies have measured direct wrench time to be around 30 percent of a craft-person's day. The other 70 percent is field coordination and travel about the site. While field coordination and travel are part of the job, LEAN Construction aims to increase direct wrench time by reducing inefficient or unnecessary tasks.
Waiting or Idling Waste. Just as GPS navigation reroutes drivers around slow traffic, data allows construction managers proactively manage work based on upcoming tasks, weather forecasts and the availability of materials, equipment and personnel. Real-time data takes this a step further, allowing tactical decisions to be made on short notice. Managers or superintendents no longer need to wait for communication from their teams to take a reactive action. Instead, with projects that implement real-time data analytics, managers can make proactive decisions using the real-time data for tactical awareness of field activity and unused resources.
Transportation. The supply chain, from source vendor or shop to the installed location, is a system that involves a series of steps and is ideally aligned with the path of construction. In reality, extra steps are introduced because the supply chain and path of construction often fall out of sync throughout the course of the project. Each extra step introduces additional cost and delays the completion of the project. With real-time data, managers can keep an eye on both systems, monitoring each moving piece to identify misalignments before they happen. This allows management to prioritize and address the most important issues to keep the work-fronts moving on schedule with reduced additional cost.
Unused Talent. Some interruptions result from reduced direct wrench time and keep workers from applying their talents, skills and knowledge efficiently. These interruptions are common to every project and include meetings, field coordination and unexpected issues that arise. Without data analytics, it is impossible to track, identify and mitigate recurring issues. With data analytics, management can track the root cause of an issue in real time as well as use information from current and past projects to identify upcoming issues, highlighting the work-fronts at risk of delays. This allows management to proactively mitigate issues interfering with field productivity and increase schedule confidence.
Motion. This LEAN principal aims to reduce travel times by optimizing the site layout to promote the availability of tools, materials and similar project support infrastructure. This impacts every single tradesperson on the work front. Traditionally, management did not have travel times on their radar as there was no way to capture that information. For example, these inefficiencies can include unnecessary trips to the tool shack or the permit office and long travel routes to and from the lunch trailers. They make the tradesperson’s job harder by taking them away from their specific task. While unavoidable, this reduces time-on-tools and introduces safety risks.
Data science works in tandem with project methodologies such as LEAN Construction to have a meaningful impact on waste and inefficiency. Construction and maintenance projects continue to become more complex, especially as companies are required to do more with much less. The global COVID-19 pandemic has only exacerbated this situation. LEAN Construction principles, combined with evidence through data, ultimately help to minimize these complexities and streamline operations to result in improved quality of work, worker engagement and return on investment.
Closing the Loop
Construction managers are responsible for an incredible number of tasks and subtasks, all while trying to stay on schedule and keep the costs down. Inefficiencies impact every person on site. Reducing them allows everyone to do more of what they are good at, increasing productivity and job satisfaction. The feedback loop for identifying inefficiency, implementing safeguards and measuring improvement can traditionally be very long. In fact, realizing the efficacy of new processes can span multiple projects, making it even more difficult to understand true productivity gains. In many cases, it may be impossible, leaving management guessing and resulting in loss of confidence of workers doing the work.
Data science offers a much faster feedback loop that eliminates subjective opinions or guesswork. Grounded in evidence, real-time data allows construction managers to determine whether their productivity measures were effective in a matter of days and attribute increases in efficiency to a specific action. This process respects the teams in the field, ensuring their services are confidently generating more value. Data science equips construction and turnaround project managers with visibility into project bottlenecks, the agility to make real-time adjustments and the advantage of seeing immediate results. Interactive reporting shows time-on-tool for current projects and can be used as comparison for future projects to help set schedules, stay on track and develop workforce policies.
Connected technology and data science are key to successful large-scale construction and turnaround projects. It is one example of how digital transformation continues to reshape how companies operate, optimize performance and keep their people safe. It is what keeps a company competitive and ensures their operations are sustainable.
This article originally appeared in the September 2020 issue of Occupational Health & Safety.