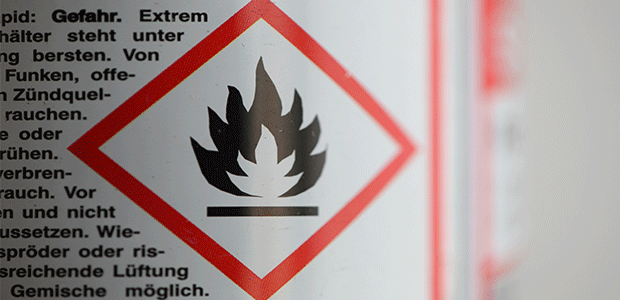
Get the Upper Hand on GHS Label Compliance
Simple SDS-to-label compliance cross-checks, expert design tips and more.
- By JoAnn Mrgich, Colwin Chan
- Feb 01, 2021
OSHA required businesses to transition to Globally Harmonized System (GHS) standards for chemical safety and hazard communication in 2016. While most employers are now informed and working within the new standards, it can still be difficult to find the exact information needed to create compliant GHS labels.
For the average facility, if a primary container label is damaged or illegible, creating new ones that are GHS-compliant are often a pain for safety and compliance teams. Yet, GHS compliance is critical if the chemicals will be distributed, transported or even transferred between facilities.
This article covers a brief overview of Safety Data Sheets (SDS) and how to find required GHS label information, use SDS to quickly check GHS compliance and design effective and compliant GHS labels.
A Brief Overview of Safety Data Sheets and GHS Compliance
Safety Data Sheets are a summary document covered in OSHA standard 1910.1200(g). They include a wealth of information about the physical, health and environmental hazards of each chemical as well as how to safely store, handle and transport them.
The information included in SDS is organized into 16 sections for easy navigation. The 16 sections are further organized in the following manner:
Sections 1-8: General Information. For example, identifying the chemical, its composition, how it should be handled and stored, exposure limits and what to do in a variety of emergency situations.
Sections 9-11: Technical and Scientific Information. The information required in these particular sections of the safety data sheet is very specific and detailed, including physical and chemical properties, stability, reactivity and toxicological information.
Sections 12-15: Information Governed by Non-OSHA Agencies. This includes environmental information, disposal considerations, transportation information and other regulations not indicated anywhere else on the SDS.
Section 16: Other Information. This section can include any useful information that hasn’t been recorded elsewhere on the SDS as well as information about the SDS itself. For example, facts such as when the SDS was prepared, the last known revision date, and where changes were made in the most recent revision could be included.
What Information is Required on a GHS Label?
OSHA Hazard Communication Standard 1910.1200(f)(1) was revised in 2012 to include six specific elements. These six elements are in alignment with GHS standards for labeling potentially hazardous chemical containers that will leave your facility.
- Product Name/Identifier. The unique name or number that identifies a hazardous chemical
- Signal Word. “Danger” or “warning” used to communicate the relative severity of the hazard
- Hazard Statement. The nature of the hazard (for example, “causes serious eye damage” or “toxic if swallowed”)
- Pictograms. Specific, globally standardized black and white symbols surrounded by red diamonds that convey health, physical and environmental information to transcend language barriers
- Precautionary Statements. Any measures that could be employed to minimize and/or prevent the effects of the hazard (for example, first aid or PPE)
- Supplier Identification. The name, address and telephone number of the supplier.
Where to Find Chemical Information for GHS Labels
All the information required to create GHS-compliant labels is included in the SDS. However, there are three additional ways to find chemical information for replacing a GHS label: the original GHS label on the primary container, an online chemical database or a GHS label design subscription that includes a chemical database.
If the original label is intact and legible, simply copying it is a great option, though the information will still need to be manually added to the label. Using a GHS subscription for label design software that includes a chemical database can help autofill your labels if you have the Chemical Abstract Service (CAS) registry number or the chemical name.
Whichever method you choose, the most important thing you need is the SDS because you’ll need it for supplier information and to verify that the information on your label matches the SDS. If it’s missing, contact the supplier and request a replacement—the burden of providing SDS is always on the supplier.
Using SDS to Cross-check Your GHS Label Information
Although there are 16 sections on an SDS, the first three sections are all that are needed to fill out the six elements of a compliant GHS label. SDS Section 1 (Identification) includes the product name/identifier and information for supplier identification. Section 2 (Hazard Identification) includes the signal word, hazard statements, pictograms and precautionary statements.
Section 3 (Composition/Information on Ingredients) may include a CAS number, which isn’t required to include on GHS labels, but is helpful to have on hand for looking up chemical information. If the chemical is not a mixture and the CAS number was not in Section 1, it will definitely be listed in Section 3.
SDS Reference Tips for GHS Label Compliance
One way to make referencing SDS easier is to copy the table above to use an index for the exact SDS section required for each GHS label element. Posting the information in, on or near your SDS binder ensures employees who need the information can find it quickly.
You can simply print or write out the table and keep it in the SDS binder pocket or use sheet protector to add it as another sheet in the binder. Other options include printing the table on a durable label and sticking it right to the binder, or posting the information on the wall near your SDS binder station.
It’s also a good idea to color-code the SDS sections needed in order to make the information easier to reference. A few minutes spent highlighting the relevant SDS sections pays off in the long run, saving time when creating new/replacement labels and making in-house GHS label inspection more efficient.
What Should a GHS-compliant Label Look Like?
GHS pictograms are the only required chemical label elements that must look a certain way in order to be compliant. There are nine specific GHS symbols, which are black and white, surrounded by a red diamond:
- Health Hazard
- Flame
- Exclamation Mark
- Gas Cylinder
- Corrosion
- Exploding Bomb
- Flame Over Circle
- Skull and Crossbones
- Environment (which is not mandatory)
All other GHS label elements should be designed and laid out in a way that is easy for workers to read and understand. While there are no explicit font guidelines, a clean sans-serif font, large enough to read and in high contrast to any background are good practices to follow. There’s no need to get creative with fancy fonts or colors—simplicity and directness are key.
How to Create GHS Labels Without a Graphic Designer
The best way to make sure your GHS labels are optimized for communicating information and include all required elements is to use GHS label design software. Options range from free online templates to templates included with label printer software and low-cost GHS subscription services.
Most basic online GHS templates, along with those included with label printer software, generally include fields for the six required GHS elements and access to the nine GHS pictograms. With these methods, the user fills in all information manually. GHS subscription services can offer autofill options.
The Basics of GHS Durability & Compliance
If you’re shipping chemicals by sea, label durability will be paramount to achieving GHS compliance. Unlike the six GHS label elements, which are regulated by OSHA, label durability for chemicals traveling by sea is regulated by the International Maritime Organization (IMO).
The IMO requires International Maritime Dangerous Goods (IMDG) certification, which includes British Standard BS5609 for label durability in marine environments. These requirements are very stringent and require two different levels of testing in order to ensure GHS labels will remain intact and legible in overseas shipping conditions.
If you’re not shipping overseas, there are no GHS guidelines for durability. However, OSHA can issue citations if your GHS labels are missing or no longer intact and legible. Labels with strong permanent adhesive, chemical resistance and resistance to general wear and tear in heavy-duty environments are strongly recommended to help avoid citations due to damaged or missing labels.
Summary of GHS Label Compliance Tips
Safety Data Sheets (SDS) contain all the information needed in order to create a compliant GHS label. Although SDS are incredibly detailed and include 16 sections, you only need Sections 1-3 to cross-check the six required elements of a GHS label. Color-coding your SDS and using a GHS label-to-SDS reference table can help streamline in-house GHs label inspections and help ensure accuracy come OSHA inspection day.
GHS pictograms are the only design element required by OSHA, and durability compliance is only regulated by IMO if you’re shipping chemicals oversees. Aside from those two factors, label design and durability requirements are largely up to the safety and compliance team and should be optimized for effectiveness and user efficiency.
Options for creating effective GHS label designs without a graphic designer include free online templates, templates included with label printer software and low-cost GHS subscription services for online label design software. GHS subscription services can also assist with filling in GHS label information provided it includes a chemical database. Other ways to find GHS label information include the original primary container label or a stand-alone chemical database.
Following these guides can help ease points of difficulty for safety and compliance teams. Start implementing these practices today to help make it easier for your team to find required GHS label information, use SDS to quickly check accuracy and design effective and compliant GHS labels.
This article originally appeared in the January/February 2021 issue of Occupational Health & Safety.