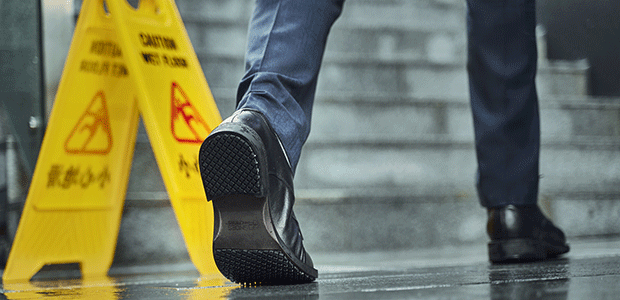
Getting a Grip on Slip Resistance
Evaluating the coefficient of friction of PPE footwear.
- By Christopher Cooper
- Feb 01, 2021
Hectic restaurant kitchens, busy hospital hallways, the debris-strewn floors of food manufacturing plants—all are undeniably hazardous work environments that multiply the chance of slip and fall accidents and injuries.
Slip-resistant footwear can help protect workers, but how is slip resistance properly evaluated?
Slip-resistant footwear has been proven to reduce slip and fall occurrence, most recently in a NIOSH study published in the Scandinavian Journal of Work, Environment & Health, but all slip-resistant shoes are not created equal. Even now, there is no standard definition of the term. What does it really mean when a shoe is labelled non-slip, anti-slip or slip resistant?
There are agreed-upon standards and best practices overseeing industrial safety toe footwear. However, and importantly, there is no consensus on an approved and enforced standard of slip- resistant protection for the general workforce. Contrast that with safety toe standards, where ASTM F2413 is the universally recognized and accepted industry standard that covers footwear for a wide range of jobs, from truck driving to warehousing to construction and manufacturing.
Servers, bartenders, janitors, chefs, grocery store clerks, clinical medical staff—all are professions that involve dangerous floor conditions. In these slick and slippery environments with contaminants ranging from grease and oil to soap, water and chemicals, safety professionals need the proper data to define and qualify “slip-resistant footwear” for employee use in their company safety programs across all industries.
The goal: approved testing methods that approximate accurate measurements of the footwear's slip-resistant safety in real-world environments.
The Coefficient of Friction (COF)
The standard method for evaluating the slip resistance of footwear is by determining its dynamic coefficient of friction (COF).
According to Introduction to Plastics Engineering, the coefficient of friction is defined as: "The ratio of the force required to move two sliding surfaces over each other, and the force holding them together." The COF can be either a static or dynamic measurement.
The difficulty in determining the slip resistance of occupational footwear in real-world environments comes from the three factors that, in combination, affect the scoring of COF:
- Floor Type
- Contaminants
- Footwear
Dynamic COF measures the force between surfaces when one or more of the objects are in motion, but herein lies the complexity. Reliable testing protocols must yield reproducible standardized results, taking into consideration the relationship between the footwear, the contaminant and the floor type.
ASTM F2913 Slip Resistance Testing
ASTM International is one of the largest voluntary standards organizations in the world. Its F2913 testing standard, developed in 2012, provides the current basis for measuring the slip resistance of footwear in action.
ASTM F2913 testing produces a measurable, reproducible result, though there is no universally agreed-upon “magic safety number” when evaluating the slip scores themselves. However, it provides valuable data in evaluating footwear slip resistance.
Though it is true that, “to date no study has been performed that defines the safe threshold COF…for all combinations of footwear, contaminant, and floor type,” ASTM F2913 offers a strong directional guideline for evaluating the effectiveness of slip-resistant footwear for the workplace and has become the gold standard in determining the dynamic COF of footwear and outsole. Here’s ASTM’s description of F2913:
This test method determines the dynamic coefficient of friction between footwear and flooring under reproducible laboratory conditions for evaluating relative slip performance. The method is applicable to all types of footwear, outsole units, heel top lifts and sheet soling materials, also to most types of floorings, including matting and stair nosing, and surface contaminants on the flooring surface, including but not limited to liquid water, ice, oil and grease.
In the F2913 protocols, COF scores are tested under the following contaminants:
- Water/Ice
- Oil
- Soap/Detergent
- Grease
- Combinations of the above
Most notably in F2913, the testing is conducted on the entire shoe, rather than a swatch or section of the outsole. Methods that don’t test the entire shoe may yield higher scores that do not accurately reflect the performance of the shoe in action. Still, other testing methods generally employ a standardized test foot primarily for evaluation of flooring.
With the advent of ASTM standard F2913, the specific testing of footwear (rather than merely floor surfaces) for slip resistance brings us closer to a testing protocol that takes those key factors—floor, contaminants and footwear—into consideration and offers a solid foundation for evaluating the slip resistance of PPE footwear.
ASTM F2913 or the Whole Shoe test provides the most complete approach to evaluating how different footwear materials interact with various work surfaces. All slip-resistant footwear should be tested to this standard to establish a common basis for comparison.
Many safety professionals and manufacturers rely upon slip scores generated through Mark II Brungraber, also known as ASTM F1677. However, this test was withdrawn by ASTM in 2006 because it only measures a portion of the outsole and not the whole shoe.
ASTM F2913 provides better data, though of course it cannot completely quantify the term “slip resistance” or fully ensure safety. As Blanchette and Spiller note, “it is important to establish that no testing, either human subject or mechanical, can accurately predict with 100 percent certainty the required level of safety so that slips will not occur.”
Reputable slip-resistant footwear manufacturers continuously test their footwear and publish their findings, utilizing up-to-date testing standards. A vendor should be able to provide the dynamic COF score of each and every shoe style they produce upon request.
Slip-Resistant Outsole Technology
Genuine slip-resistant footwear focuses on outsole technology and overall shoe design. Slip-resistant outsole technology features design elements including wide heel construction for more surface contact, proprietary compounds for a more powerful grip and a variety of tread patterns for added oil and clog resistance.
Slip-resistant outsoles should be manufactured through a process that ensures that the last shoe from the mold is as effective as the first, including:
- State-of-the-art mold-making technologies such as CnC
- Thorough mold cleaning to keep molds in tiptop shape
- Frequent checking and replacing of molds throughout the production process to ensure uniform quality
Recommendations for Safety Professionals
More and more companies have a safety footwear policy in place as part of their overall safety strategy, but enforcing them effectively does require investment and commitment. Managed programs enhance overall safety by helping to ensure compliance and adoption.
Mandated programs require the employer to provide footwear at no charge, which has been proven to ensure compliance and reduce slip-related accidents and injuries. Providing subsidized or discounted footwear to employees is generally accepted to be somewhat less effective than the total workforce coverage of a company-paid, mandated program, but is also offered by safety footwear providers as a means of cutting accident rates and minimizing loss.
Beware manufacturers who mass produce inexpensive footwear, then label it slip-proof based on superficial or cursory testing methods. Safety professionals know the difference between ordinary store-bought shoes and footwear designed specifically to withstand slippery conditions and prevent workplace accidents.
Look for a slip-resistant footwear provider that:
- Performs whole shoe testing
- Runs tests using a variety of contaminants, including, oil, water, soap and grease
- Verifies their slips scores via independent laboratory testing
- Uses internationally recognized testing methods such as ASTM F2913
Here are a few questions safety professionals can ask when considering a slip-resistant shoe provider:
- What testing methods do you employ to evaluate slip resistance?
- What are the COF scores of the footwear?
- What outsole tread patterns are appropriate to specific environments (i.e., clog-resistant for food manufacturing and preparation, cold formula for freezers and coolers, etc.)?
In choosing slip-resistant footwear for their workforce, employers and their loss and risk managers cannot afford to play fast and loose with semantic terms where the safety of their workforce and the viability of their businesses are at stake. They must have the proper data to carefully evaluate the slip-resistant safety of the footwear their workforce is wearing. Bottom line: always choose a trusted authority in the field of slip-resistant PPE footwear.
This article originally appeared in the January/February 2021 issue of Occupational Health & Safety.