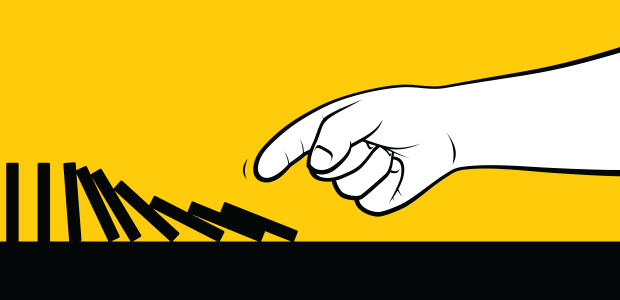
The Five Pillars of a Highly Effective Safety Management Process
The five pillars will support continued excellence in operations as well as provide a framework for achieving excellence in workforce safety.
- By Peter Furst
- Feb 01, 2021
Most businesses face the possibility of worker accidents and potential injuries. In all likelihood, they have a safety department or an assigned person to oversee and manage such possible outcomes. Traditionally, the management of safety involved complied with the company safety program. The bulk of the program pretty much regurgitated the safety standards as promulgated by the relevant State or Federal jurisdiction. Some organizations may add additional requirements to this program based on specific risks, past experience or other relevant considerations.
There were two significant pieces of governmental legislation which impacted the approach to occupational accidents and the associated attention to and management of worker injuries. The first was the enactment of workers compensation legislation by various states starting in 1911, with the last one adopting it in 1948. This brought about some level of improvement in worker safety, but the need for greater uniformity throughout the country as well as further reduction in accidents lead to the passage of the Occupational Safety and Health Act by the Federal Government in 1970.
Traditional Safety Management
With the passage of the workers compensation legislation, worker accidents and the resulting injuries had financial consequences for their employers. This created the need to understand why workers were getting injured on the job, so as to allow management to intervene in order to reduce the number of accidents and therefore control their related costs. The industry got its answer when H. Heinrich proposed the domino theory of accident causation. The theory proposed that injuries resulted from a number of interrelated and preceding factors.
Heinrich proposed that injuries were the result of a series of events that happened in sequence, and the removal of any one of the preceding events would stop the injury from occurring. He proposed five elements to this series. An occupational example:
- The first event would be the worker engaging in his task (driving nails)
- The worker swings the hammer
- But the worker makes an error and misses the nail
- The worker then hits his other hand
- The worker smashes his fingers causing an injury
Since just about every accident occurs due to some unsafe act on the part of workers, supervisors and management tried to find reason for this. These could be attributed to factors such as:
- Inattention
- Rushing
- Lack of knowledge
- Carelessness
- Distraction
- Unfamiliarity with safety or best practices
- Fatigue
- Unfamiliarity with the safety program elements
All of these pointed to some form of deficiency or negligence on the part of the worker. The more common approach to dealing with this was to provide safety training to workers and conduct more inspections.
Evolution of Safety
The management of safety evolved over time due to a number of factors. The industrial revolution created a demand for a large number of workers in factory settings. Those organizations were not terribly concerned with worker safety, as it was deemed that workers were responsible for their own safety and wellbeing.
With the passage of the Occupational Safety and Health Act, organizations were required to comply with safety standards and report results. The frequency of certain accidents or the annual risk evaluation of safety outcomes with a broker or insurance carrier caused the safety function of the organization to make certain program elements a priority in order to try to control similar accidents. Forward thinking organizations through leadership and management were able to make safety a value which not only reduced the risk of injuries but reduced their severity and, to some extent, controlled cost. The implementation of the five pillars will make safety instinctual and will help make accidents somewhat rare events.
Foundational Elements
Starting with a solid foundation the five pillars will support continued excellence in operations as well as provide a framework for achieving excellence in workforce safety. Foundationally the organizational systems, polices, procedures and practices must be integrated and aligned in order to support effective operations. The value proposition must exceed customer and partner expectations and build trustful and loyal relationships, leadership must create a supportive work environment which reduces risk, and enables worker performance, success and job satisfaction.
There has to be a robust value-based culture that fosters nurtures, supports, rewards, and values safe operations. There exists a positive leader-member exchange, with organizational justice, mutual trust and respect, along with excellent communication fostering cooperation which results in efficient and effective operations. In a value-based organizational culture, everyone leads from core principles, contributes to safe operations, is involved and champions the safety and health of all involved. This will, and should make safety processes, procedures and practices instinctual.
The Five Pillars framework for Excellence
The five pillars then provide the framework that creates an innovative, excellence driven, business focused approach to addressing challenges and fostering the implementation of a robust safety management process.
Business & Operational Excellence. Business and operational integration is crucial to the creation of efficient and effective systems which allow for and support an injury free workplace. The internal systems, processes and procedures must be in harmony and all work towards the creation of a risk and injury free workplace. This internal alignment drives a 360 degree focus horizontally, vertically and inside to outside the organization approach. The outside factor involves the value chain partners, vendors and suppliers. They need to be in alignment with the organization’s systems in order to further excellence in all aspects of the business. It also involves partners cooperating and delivering on their promises with flawless execution, which reduces risk and supports the safety and health of all workers.
Relationship, Trust, & Value Proposition. In many industries there is a long value chain populated by a number of organizations, all of which have to ensure the achievement of common interest objectives by cooperating in order to accomplish their common goals. They have to make sure they deliver on their promises in order to build trust. Trust is critical to every business exchange and a key factor in influencing behavior. Organizations may need to clearly present their value proposition which should stress fair treatment, ethical behavior, cooperative problem solving, etc. in order to build effective, harmonious, interdependent and trusting relationships. Trust could play a key role in the management of safe operations as well as fostering the safe behavior of involved individuals.
Principle Focused Leadership. Leadership is a key element in creating and sustaining a value-based organizational culture, which supports and fosters excellence. Principle-focused leadership involves:
- Creating a positive, enabling and satisfying work environment
- Ethical behavior
- Inspiring a shared vision
- Innovative thinking
- Encouraging followers to engage
- Challenging the process
- Fostering learning and growth
- Leading positive change
It also means creating an open, safe, trusting and empathic work environment based on a positive leader-member exchange, creating a safe and healthy worksite.
Innovation, Growth & Learning. Innovation, growth and learning are important because of the nature of modern business. Just about the only constant in business is that change is inevitable, and change is occurring at faster rates than ever. So, the organization has to understand its environment and learn from it so as to change its internal processes and procedures, foster growth and remain competitive. The innovation continuum includes efficiency, evolutionary and revolutionary innovation. Growth involves increased knowledge and understanding of the employees, thereby enabling them to effectively operate and support the internal integration and alignment necessary to create the injury free workplace.
Dashboards & Metrics. To effectively manage you need to measure. Senior management understands that the measurement system influences organizational behavior. Effective measurement has to be predictive as well as prescriptive in nature if it is to provide information for managing performance. Another thing that contributes to difficulty or complexity is that often important factors tend to be hard to measure consistently and objectively.
The scorecard also serves to bring together into one report several important but seemingly diverse aspects of the business. Another important aspect of the organizational scorecard is that it creates a platform for alignment within the organization. This is important to strategy deployment as well as guarding against sub-optimization. A robust scorecard represents all the important operational measures holistically.
Conclusion
Excellence in safety can only be achieved through a strategy-driven, performance-based safety management process that is supported by operational excellence, driven by principle centered leadership, sustained by engaged and involved employees and facilitated by a value-based culture. Obviously, we need to approach the process holistically. Safety should be fully integrated into the organization’s operations, and safety outcomes should be aligned with business goals. Therefore, the safety process will become woven into the very fabric of the organization and become instinctual. Achieving an injury free workplace will naturally flow from the operational activities.
This article originally appeared in the January/February 2021 issue of Occupational Health & Safety.